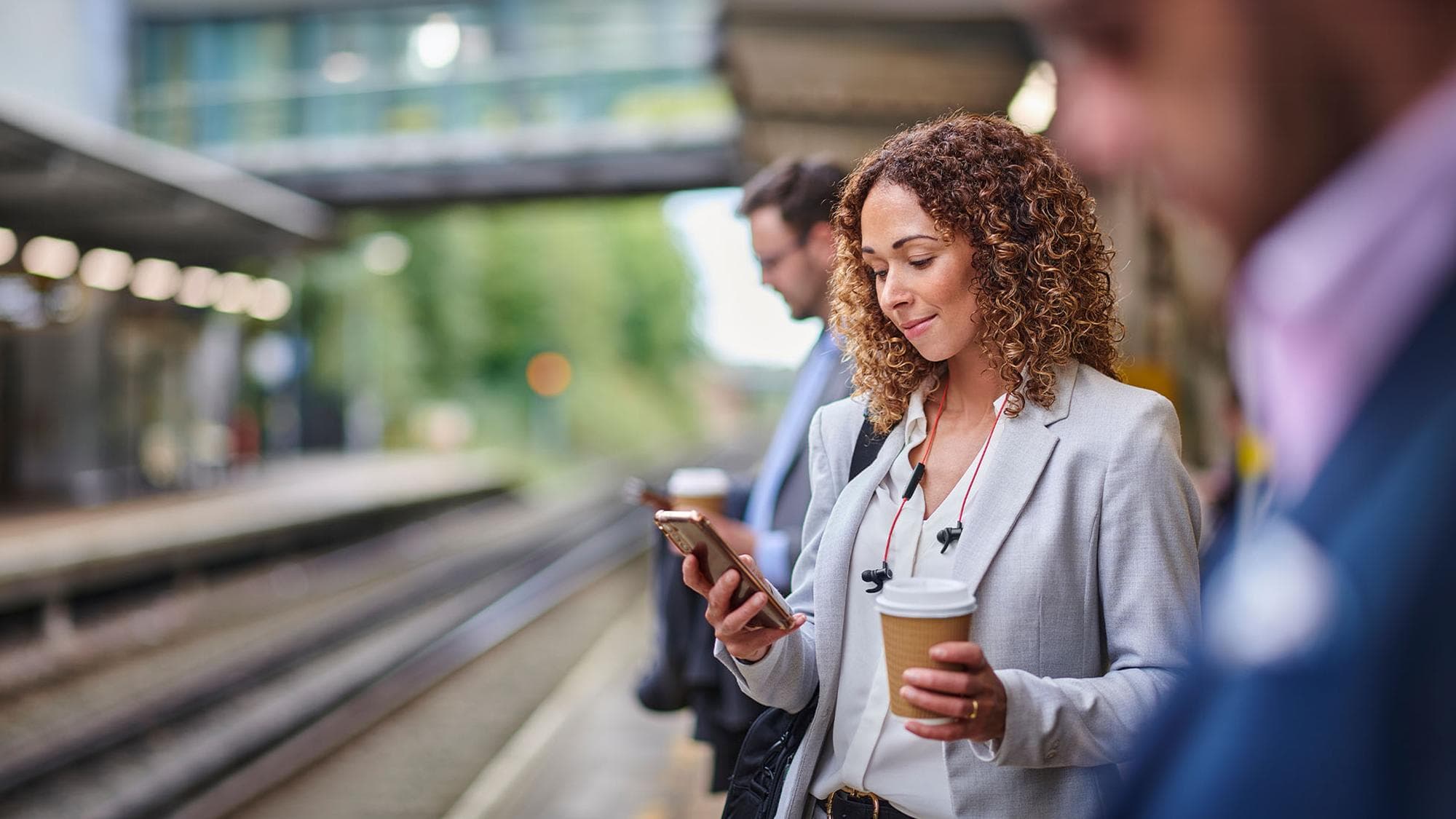
News
Keeping you updated on timely matters is important to us. Our featured newsletters are specific to Individual and Business, Construction, Healthcare, Manufacturing and Not-for-Profit. Check back often to read the news that is important to you. Or better yet, sign up to have the newsletter(s) emailed right to you!